News
2018 GÜNTHER Technology Days

Two jam-packed days dedicated to efficient hot runner technology
The 10th annual Technology Days event was held by GÜNTHER Hot Runner Technology in Frankenberg (Eder), Germany on September 26 and 27, 2018. On each of the two days more than 300 visitors learned about opportunities for increasing efficiency in the injection moulding field from the leader in hot runner technology. Networking and information exchange also took center stage.
Encouraging growth spurs investment
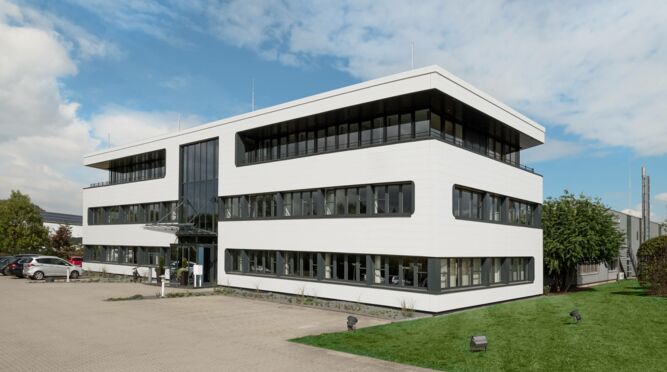
GÜNTHER Hot Runner Technology has customers all around the world in the electronics industry and packaging technology, medical technology, consumer goods and car manufacturing sectors. “We’ve been continually expanding our sales network for years, which has had an encouraging and positive effect on our order books,” commented Managing Director Siegrid Sommer during the opening ceremony of the Technology Days event. The Frankenberg-based company’s plethora of patents and new developments attest to its innovative power. “Our products and solutions open up new opportunities to injection moulders and mould makers, enabling them to produce with lower tolerances, higher quality & process reliability, faster and more cost effectively. To reliably ensure and continue to increase the high quality of our hot runner nozzles and systems, it’s only natural that we continually invest in our machine park and infrastructure.” The company invested just under 3 million euros in a new cylindrical grinding machine, two CNC lathes (index and Benzinger) and an additional screen printer for thick-film production. “We think it's important that all machines are automated and networked with one another to enable us to plan in a more precise way to ensure shorter delivery times and to improve our processes, as well as to increase our quality standard even more,” explains Horst-Werner Bremmer, Head of Sales at GÜNTHER Hot Runner Technology. The many visitors to Technology Days were able to see this for themselves on guided company tours.
Expanding and deepening expertise

24 innovative specialist presentations from both external and in-house speakers were held in the newly redesigned and extended administrative building. In the pleasant atmosphere of the spacious seminar rooms, which radiate a light, bright and friendly atmosphere thanks to the combination of wood and glass used in the building's construction, it was easy for attendees at the specialist presentations to follow the speakers’ explanations.
These included the presentation on energy efficiency in the temperature control of injection moulding tools given by Albrecht Weipert from HB-Therm. The main task of a temperature control system is to draw away heat introduced by the molten plastic so that the component shape remains stable – and there is hardly any potential for savings here. Albrecht Weipert demonstrated where and how potential for savings can be identified and energy efficiency increased. Markus Raffelsieper from Kistler explored digitization in the injection moulding environment. This enables established processes to be easily transferred from one machine to another with assistance systems which operate on the basis of the mould cavity pressure. It also enables optimum utilization of the switchover point from the injection phase to the holding-pressure phase despite material and machine fluctuations.

Complex geometries and quality characteristics and their correlation to the mould cavity pressure can also be predicted and monitored with assistance systems. Mathias Lupberger, a project manager at Braunform, sketched out applications with low part weights which were processed using multi-component technology. His motive for multi-component technology was, among other things, enhancement of the end product and the creation of a function. The individual customization of tried-and-tested multi-component mould technologies was covered in the talk. Torsten Schnell of GÜNTHER Hot Runner Technology described solution options for micro-injection moulding with a hot runner using example applications, taking dwell time and temperature management into account. He demonstrated the requirements placed on the hot runner system and the prerequisites which the hot runner system has to meet in connection with the injection moulding machine and mould.
Many other presentations by AHP Merkle, Arburg, ALLOD Werkstoff, Contura MTC, K.D. Feddersen, Kunststoff Institut Lüdenscheid, Konstruktionsbüro Hein, MMS Modular Molding Systems, Netstal, OECHSLER, SIGMASOFT, Polymer Training and Innovation Center, Stemke Cooling Systems, toolcraft and Uddeholm und Wacker completed the series of lectures held in German and English.

Over the entire course of two days, the trade show featuring a multitude of companies was always an attraction, offering the opportunity for networking, talking shop and exchanging interesting information on mould and hot runner technology as well as the injection moulding process itself. Visitors also met for smalltalk and networking in front of the striking large new plant wall in the waiting area of the third floor of the administrative building.
Managing Director Siegrid Sommer was extremely satisfied with the event: “Once again, we saw that technological development in the plastics industry is proceeding at full speed. Every day, new innovations are opening up unimagined possibilities for product manufacturing, and we will be accompanying this process with our 35 years of experience in hot runner technology. The large number of participants is also an indication of our importance as a leading innovator and problem solver. I’m already looking forward to the next Technology Days event.”